Shifting, House?
✔
Lowest Price Quote✔
Safe Relocation✔
Professional Labour✔
Timely Pickup & Delivery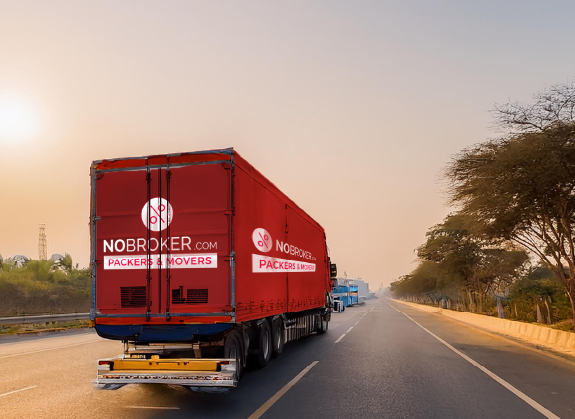
Intercity Shifting-Upto 25% Off
Check Prices
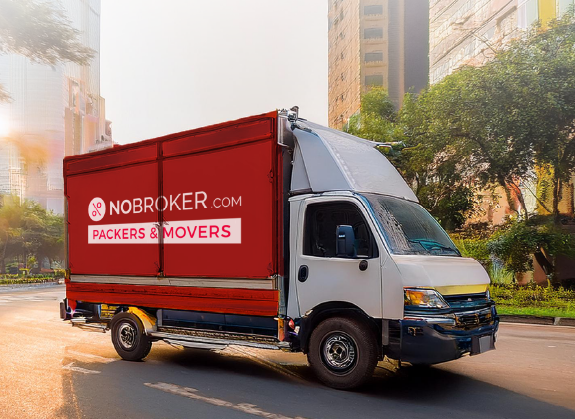
Intracity Shifting-Upto 25% Off
Check Prices
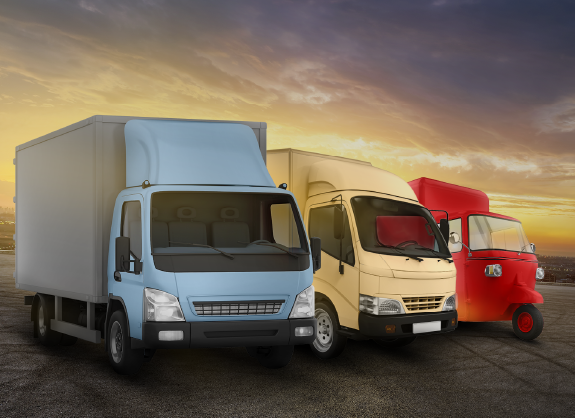
City Tempo-Upto 50% Off
Book Now
Shifting, House?
✔
Lowest Price Quote✔
Safe Relocation✔
Professional Labour✔
Timely Pickup & Delivery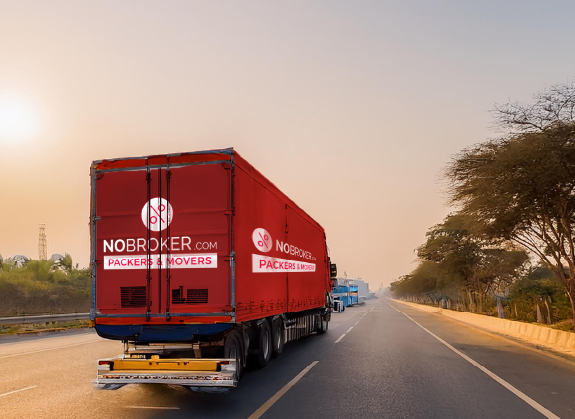
Intercity Shifting-Upto 25% Off
Check Prices
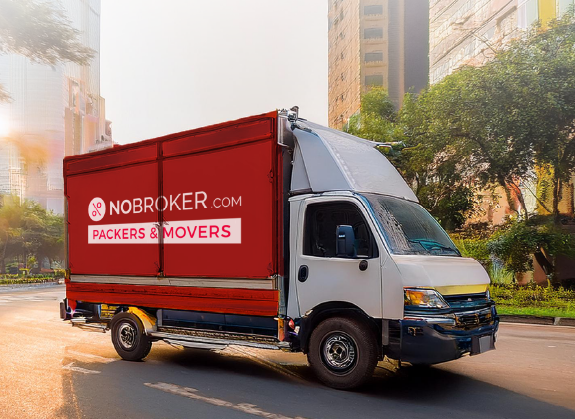
Intracity Shifting-Upto 25% Off
Check Prices
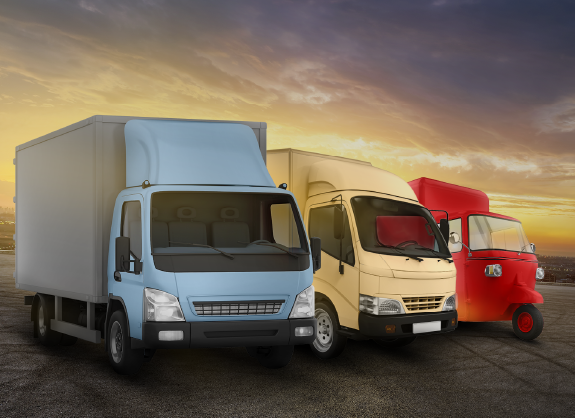
City Tempo-Upto 50% Off
Book Now
Enameled wire is a category of magnet wire, generally refers to the insulated wire used to make coils or windings in electrical products. Also called winding wire.
Magnet wire meets a variety of application and manufacturing process requirements. The former includes its shape, specification, ability to work at high temperature for short and long periods of time, as well as to withstand intense vibration in some occasions and centrifugal force at high speed, resistance to corona and breakdown under high voltage, and resistance to special atmospheres. Chemical corrosion, etc.; the latter includes the requirements of stretching, bending and abrasion during winding and embedding, as well as swelling and erosion during dipping and drying.
Magnet wires can be classified by their basic composition, conductive core, and electrical insulation. Generally, it is divided into enameled wire, wrapped wire, enameled wrapped wire and inorganic insulated wire according to the insulating material and production method used in the electrical insulating layer.
The enameled wire is made by coating the conductor with the corresponding lacquer solution, and then through the evaporation of the solvent and the curing of the lacquer film and cooling. The enameled wire can be divided into polyester enameled wire, polyesterimide enameled
wire, polyamideimide enameled wire, polyimide enameled wire, polyesterimide/polyamideimide enameled wire, corona-resistant enameled wire, and oily enameled wire according to the insulating paint used. Paint, acetal paint, polyurethane enameled wire, etc. Sometimes it is also classified according to the particularity of its use, such as self-adhesive enameled wire, refrigerant resistant enameled wire, etc.
The early enameled wire was oily enameled wire, made of tung oil and so on. The paint film has poor properties and cannot be directly used to make motor coils and windings. It needs to be wrapped with cotton yarn when using. Later, the polyvinyl formal enameled wire was introduced, and its mechanical function was greatly improved, and it could be directly used in the motor winding, which is called high-strength enameled wire.
With the development of weak current technology, self-adhesive enameled wires have emerged, which can obtain coils with better integrity without dipping and baking. However, its mechanical strength is poor, and it can only be used in micro motors and small motors. In addition, in order to avoid the trouble of removing the paint film first during welding, the straight-solderable enameled wire is developed, and the paint film can fall by itself in the high-temperature tin enamel tank, so that the copper wire can be easily welded.
Because the application of enameled wire is becoming more and more extensive, and the requirements are becoming more and more severe, composite enameled wire has also been developed. The inner and outer paint films are composed of different polymer materials, such as polyesterimide/polyamideimide enameled wires.
An important type of winding wire. In the early stage, cotton yarn and silk, called yarn-covered wire and silk-covered wire, were used in motors and electrical appliances. Because of the large insulation thickness and low heat resistance, most of them have been replaced by enameled wires. Now only used as high frequency winding wire. In the large and medium-sized winding wires, when the heat resistance level is high and the mechanical strength is high, the glass-wrapped wire is also used, and appropriate adhesive paint is used in the production.
The paper-covered wire still occupies an appropriate position in the wrapped wire, and is mainly used in oil-immersed transformers. The oil-paper insulation formed at this time has excellent dielectric function, low price and long service life.
Shifting, House?
✔
Lowest Price Quote✔
Safe Relocation✔
Professional Labour✔
Timely Pickup & Delivery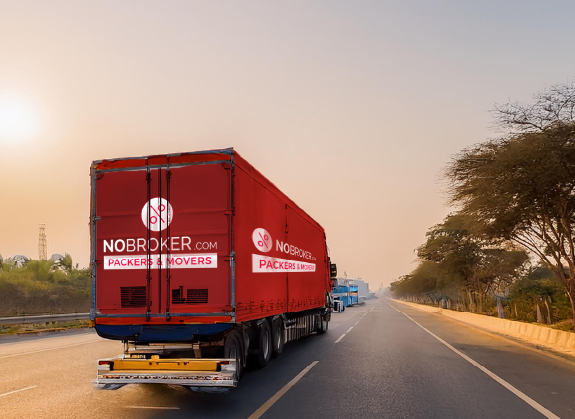
Intercity Shifting-Upto 25% Off
Check Prices
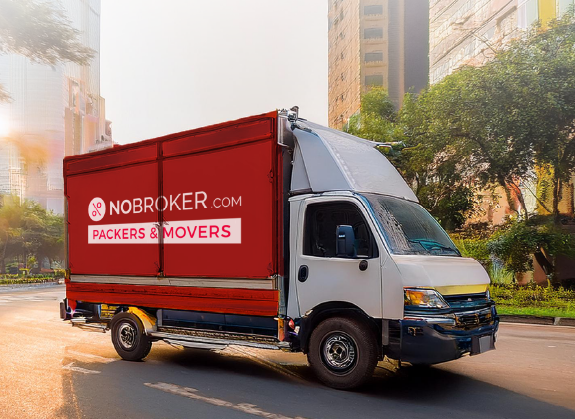
Intracity Shifting-Upto 25% Off
Check Prices
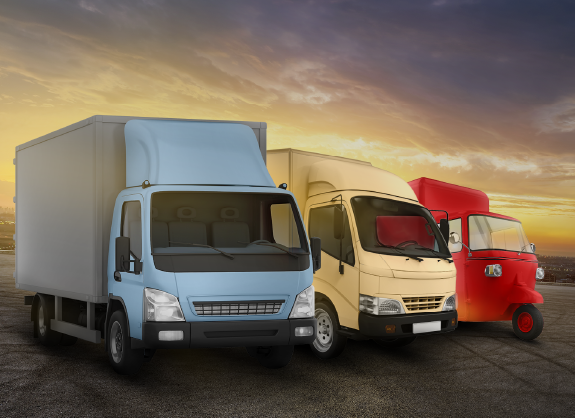
City Tempo-Upto 50% Off
Book Now
Hey buddy,
I have also used enamelled wire before, so I can tell you that it offers several advantages for electrical appliances. Also known as magnet wires, these enamelled wires refer to copper or aluminium wires that have been given a coating. This thin layer of insulation makes the wires useful for building transformers, electromagnets, speakers, hard disk actuators, motors, inductors, etc. They are also useful because they can be soldered easily.
Get Assured Cashback by Paying Your Electricity Bills via NoBroker
You should read these answers too:
Which type of electrical wire is used in houses?
Which company wire is best for house wiring?
Shifting, House?
✔
Lowest Price Quote✔
Safe Relocation✔
Professional Labour✔
Timely Pickup & Delivery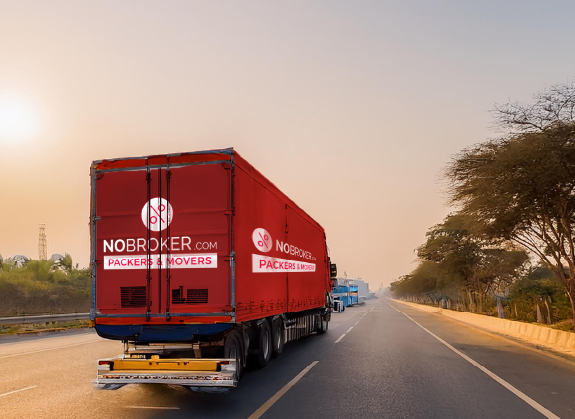
Intercity Shifting-Upto 25% Off
Check Prices
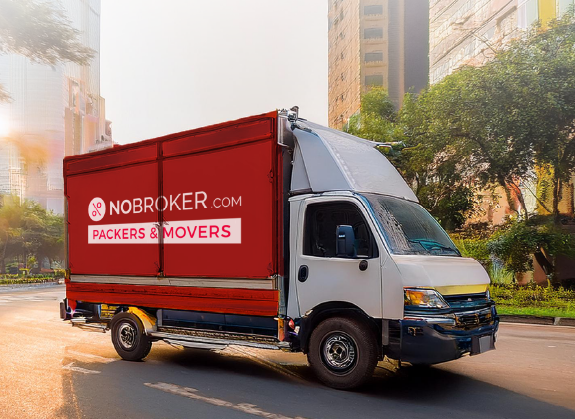
Intracity Shifting-Upto 25% Off
Check Prices
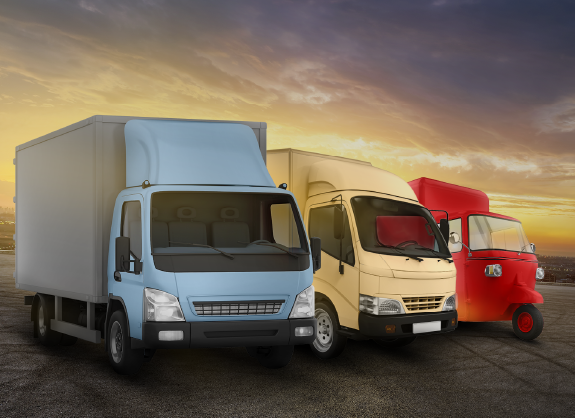
City Tempo-Upto 50% Off
Book Now
Most Viewed Questions
Recently Published Questions
Authors Of The Question
Recently Answered Questions
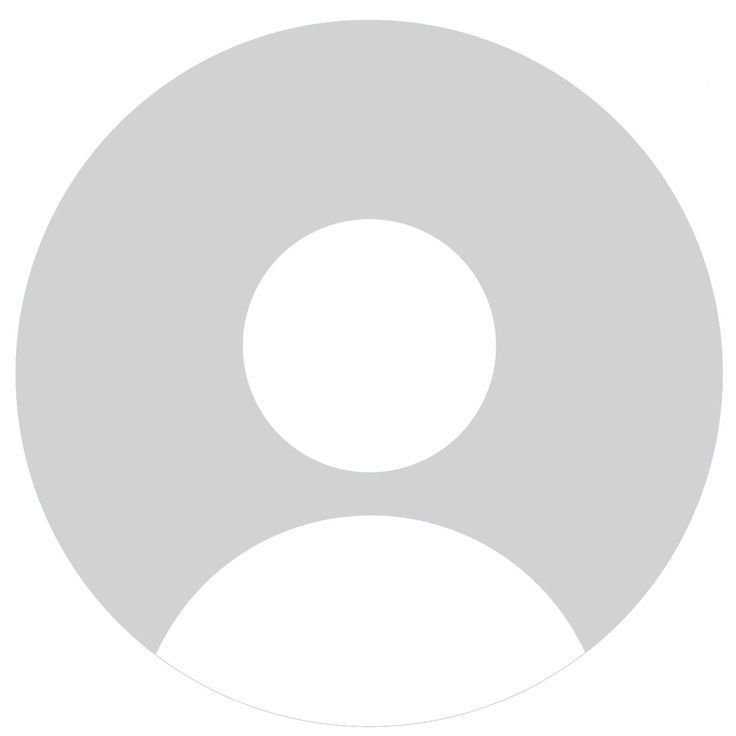
0 Total Answers
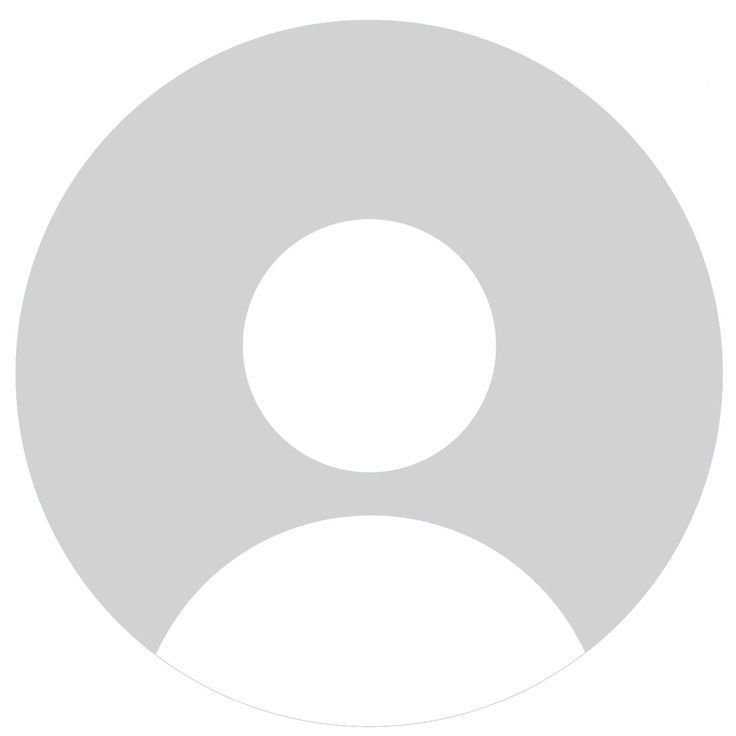
0 Total Answers
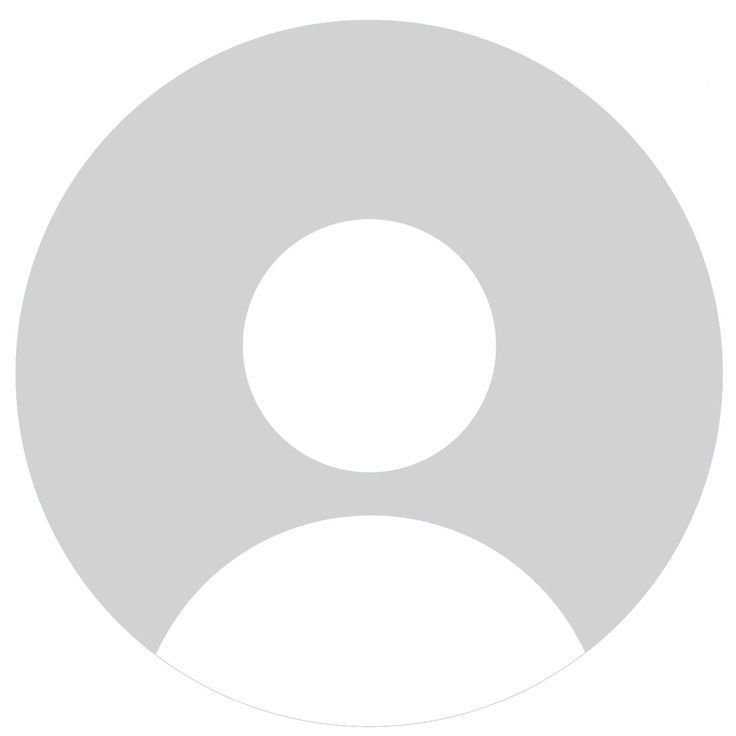
0 Total Answers
Why choose enameled wire?
Anonymous
135Views
2 Year
2022-07-25T14:30:15+00:00 2022-07-25T19:06:13+00:00Comment
4 Answers
Share